The
purpose of this page is to explain, in detail,
how to check and adjust the valves on a KLR650. This is intended
for people with modest mechanical skills, and/or those who have
never undertaken a job such as this; I made an effort to be very
specific about each step. |
This
is not a quick-start guide by any means, but
rather is intended for people who are interested in doing their
own work, and who prefer to work with a guide that spells out
each step of the process. |
|
Getting
Started. |
Make
sure the engine area is cleaned of dirt, or anything that might
find it's way into the engine once the valve cover is off.
Set up the bike on a stable surface in an area where you'll be comfortable
working for a while, an area that is as free from dust, bugs and
whatever as possible. The engine must be cold before
you can accurately check & adjust the clearances; generally,
sitting overnight is best. |
Tools. |
You'll
need an assortment of shims to cover any likely situation. Fred
at www.arrowheadmotorsports.com
carries a 16 shim set that is perfect for this, or you can get single
shims if you prefer. You'll want a good ratchet and a metric
socket set that includes 10,12 and 19mm sockets, and probably a
couple different extensions. Feeler gauges from .002"
to .012", tweezers and/or jewelers flat screwdriver and/or
surgical "Kelly" clamp to get the shims out of the "cup",
philips head and regular screwdrivers, non-drying silicone sealant
such as Yamaha Quick Bond. |
The
Procedure. |
01. |
Turn
the fuel petcock to OFF. |
02 |
Remove
both side covers - 2 philips head screws each cover. |
03. |
Remove
the saddle hold-down bolts - 1 bolt on each side. There is a plastic
"U" prong on the bottom front of the saddle that slips
under a bracket, lift the saddle back up and pull the whole thing
back to remove. |
04. |
Remove
the right radiator shroud - 2 bolts at radiator, 1 philips head
screw at the top. |
05. |
Remove
the left radiator shroud - 2 philips head bolts backed by nuts at
the shroud, 1 philips head screw at the top. |
06. |
Remove
the vent hose from the back of the gas tank. |
07. |
There
are 2 hoses to remove at the fuel valve/petcock: the gas hose, from
which gas will come out, and a smaller vacuum
hose up a little and behind it. |
08. |
Remove
the 2 mounting bolts holding the back of the gas tank to the frame.
There are 2 sideways "U's" on the underside of the gas
tank that hold it on 2 frame mounted studs. Lift the back of the
tank slightly up and pull toward the back of the bike. A
full tank of gas weighs about 35 pounds, be prepared to hold the
weight. |
09. |
Remove
the 2 rubber "bumpers" on the gas tank mounting studs;
this will improve clearance for the valve cover removal. |
|
|
|
10. |
The
pictures above show the cooling fan mounted to the left side of
the radiator using 3 bolts, and bungee corded out of the way. Remove
these 3 bolts, and tie or bungee the fan out of the way. You can
also unplug the gauge wire, circled in red, at the bottom of the
radiator, beneath where the cooling fan was, to remove the entire
assembly. |
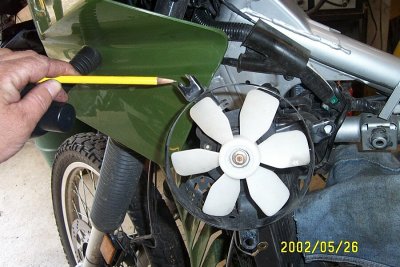 |
Thanks
to Dan for the picture above. Here's what he had to say: The
cooling fan has one bolt that is a PITA to install. By notching
the hole, I leave the bolt in and just slide it into place. |
|
11. |
Unplug
the spark plug cap from the spark plug, but leave the spark
plug in place. The spark plug cap and wire are shown above
by the cyan arrow. The red circle shows one of the gas tank bumpers
that I forgot to remove, but will remove before the cover
comes off. |
12. |
Unplug
the sensor wire. The sensor wire is shown above by the yellow arrow. |
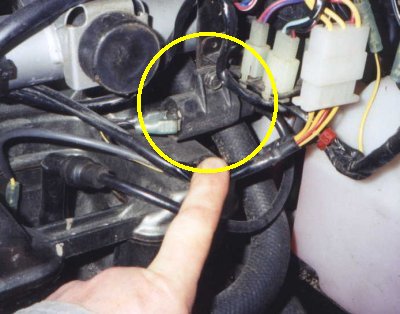 |
13. |
The
coil, shown above in the yellow circle, is mounted by one bolt on
the right side of the engine, above and forward of the spark plug
area. The spark plug wire is attached to one end of the coil, and
2 "spaded" wires are attached to the other. Remove the
bolt and tuck everything out of the way. |
|
14. |
To
make the valve cover removal easier, remove the upper engine bracket,
shown above by the large arrow. This is 2 Dorritos-shaped plates
bolted to either side of the frame and engine using 2 bolts at the
wider top, and one at the more narrow bottom. The bottom bolt has
been treated with red, high strength Loctite, and screws into a
small, heavy piece of flat stock on the left side. Remove the 3
bolts, 2 dorrito plates and small flat stock. This is not a necessary
step, but it will make your life much easier if you do it. |
|
15. |
The
picture above shows that the path has been cleared for the valve
cover removal. The radiator hose on the right side of the picture
could be removed, but is very flexible and is easily
pushed out of the way as the cover comes out. To make your life
easier, move the wiring out from under the large frame tube that
runs directly over the top of the engine. You may have to cut the
ty-wraps to do it, and if you have replacements for them, or suitable
tape, it's much easier to just snip them off. Like step 14,
this is not a necessary step, but it will
make your life much easier if you do it. NOTE:
The cover is removed from the LEFT side, and comes out easier if
you move it a little toward the front of the bike, (pushing into
the soft radiator hose a bit), and then up and out. |
|
|
16. |
Now
for the valve cover. The right side valve cover bolts are
right out in the open, but the left side ones are another story.
The above UPPER picture shows the frame-mounted
wire clamp that can be removed to allow the wiring harness to be
moved away from the frame tube. The above LOWER
picture shows sockets with extensions on the two left side valve
cover bolts. If you use straight extensions
such as these, they will not affect the accuracy
of a torque wrench. DO NOT use a swivel,
crows foot, or cheater pipe on the torque wrench handle as these
will cause inaccurate torquing. I suspect it doesn't
matter at all, but I would suggest removing the bolts in an "X"
pattern; upper left, then lower right - upper right, then lower
left. I would also suggest you use this pattern as you unscrew the
bolts 1/4 turn each until loose. (I think all this helps keep the
cover perfectly flat.) |
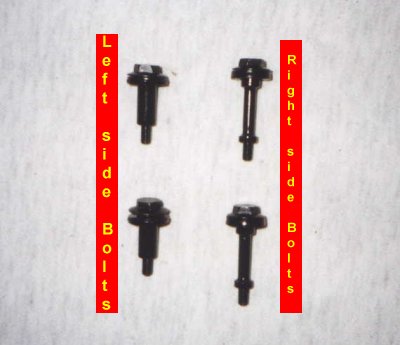 |
17. |
(The
picture above shows the valve cover bolts, and which side of the
engine they go on.) With all the valve cover bolts out, the valve
cover is ready to be popped off. Kawasaki uses, (and therefore,
shouldn't we all use it!?), a non-permanent silicone sealant to
ensure a leak-free assembly. Slight force will
be required to remove the cover; I put my hands on either side of
the engine just below the valve cover and use the force of my thumbs
to exert an upward, alternating rocking force. Warning! The valve cover and engine top are precision
machined surfaces, DO NOT pry the valve cover with anything
- scratches or gouges in either surface would be an extraordinarily
bad "mod!" |
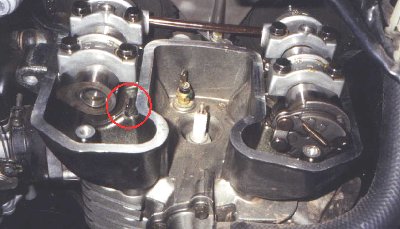 |
NOTE:
The
picture above shows the top of the engine with the valve cover
off. You've got to work for it, but about in the center of the
red circle is a slot in the "cup" that hold the shim.
You can easily turn this "cup" until the slot is easily
accessible - this is where you'll use a fine screwdriver, or tweezers
to lift the shim out once the lobe has been lifted.
You
can also break the oil suction, and get the shim out more easily
if you direct a short blast of air from an air nozzle at the cutout
in the bucket. Be ready to prevent the shim from becoming a frisbee
in case too much air is applied. |
|
Let's
establish some basics: |
First.
Left and Right is not a matter of perspective, or position;
everything has only one left side and one right side. Sitting on
the bike, facing forward, left is left and right is right. |
Second.
The intake is the back / carb side of the engine. The
exhaust is the front / headlight side of the engine. Looking down
at the top of the engine you'll see the 4 cams with shims underneath
each one. They are: |
Front
Left = Left Exhaust <> Front Right = Right Exhaust <>
Back Left = Left Intake <> Back Right = Right Intake
|
|
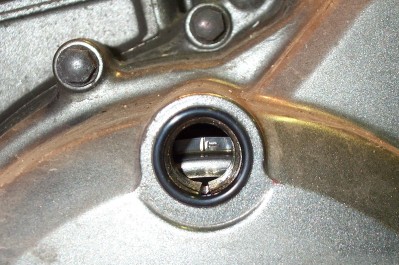 |
18. |
The
picture above shows the Top Dead Center mark, TDC. On
the lower left side of the engine, in the area just forward of
the gear shift, are 2 round plastic slotted covers - a large one
in the middle and a smaller one above it at the top. Both of these
need to removed. A deep-well socket, or one with an extension,
is used to turn the "nut" in the center hole counter-clockwise.
Warning!
Do not try to turn clockwise. If you miss the timing mark, even
by a hair, go around again.
You'll
be watching for two things here; stroke and TDC mark. While turning
the socket counter-clockwise, watch the intake cams and their
valves. The cam will come around (counter-clockwise), and the
more narrow tip of the cam will push the valve open, and then
release the valve and allow it to close. You're getting
close.
As you
slowly continue to turn, the cam tip will begin to release the
valve and allow it to open. Now, look into the smaller upper hole
that you removed the plastic cap from. You're looking for the
3rd of three marks, and they aren't far apart. First you see I,
and then F, and finally the one you want, T.
The leg of the T should be perfectly lined up
with the notch cut in the bottom of the hole. Top Dead
Center!!
Note:
At this point the marks on the camshaft sprockets point forward,
and line up with the surface of the cylinder head. |
|
At
this point, save yourself some work and just check the clearances
to see where you are, it's entirely possible that everything will
be alright and you won't have to do a thing. It's very important
that you keep careful track of all the measurements, before and
after. I designed a form that has proven to be quite useful, and
is available from the "Forms" page of this website, or
just click HERE.
The specification for the valve clearances is as follows: |
Intake:
0.10mm 0.20mm (0.004in 0.008in)
<> Exhaust: 0.15mm
0.25mm (0.006in 0.010in) |
|
I
feel there are too few riding days to waste tinkering with a bike.
With that thought in mind, and with the knowledge that the valve
clearances will close up over time, I suggest setting the valve
clearances close to the top of spec and evening them out as much
as possible. You've already got everything stripped down for the
job, why not just do it and not have to think about
it for another few thousand miles!? |
|
 |
19. |
Checking
the valve clearances is pretty easy. Use good quality, brand-name
feeler gauges. They offer feeler gauges in the range that we need
in a few different forms; regular size flat, small size flat, and
regular size with a bend near the end; get whatever works best for
you. (I like the ones with the bend at the end.) Start with
a feeler gauge about in the middle of the spec for the cam clearance
you're checking, and use larger or smaller ones until you get that
"just right" fit. Be absolutely sure to
correctly record each of the four clearances; again, the
chart HERE
is perfect for this. If things are OK the way they are, just button
it all back up - if not, continue on... |
|
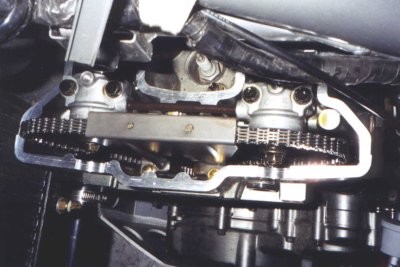 |
Warning!
The Abyss, (shown above.) This is a part of the procedure where you can't be
careful enough. A wrong move here that allows a cap locator or screw
to fall down into the engine has made men go crazy, women faint,
and children cry. (Undocumented information.) Those cap locators
can fall out immediately as you lift up the caps, or trick you and
not fall out for a couple seconds. Save yourself all kinds of heartache,
and stuff clean, lint-free towels down in and around that left side
of the engine, and don't remove them until the caps are secured
back in place. |
|
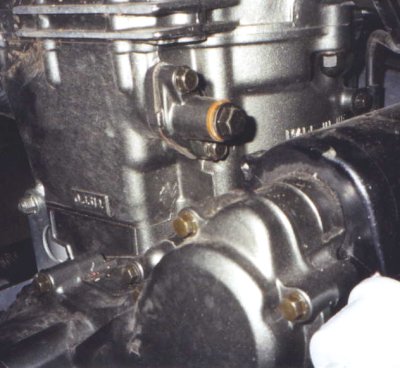 |
20. |
The
Cam Chain tensioner bolt is shown above.
Ok, the abyss is no longer an abyss, you're at TDC, have all 4
clearances correctly recorded, and are ready to proceed.
On the upper left back side of the engine you'll find the cam
chain tensioner - a larger center bolt head, (12mm), in a neck
secured at the base to the engine by two smaller bolts, (10mm.)
Remove only the 12mm center bolt, which is holding in a long,
compressed spring. Be careful, as you remove the bolt, that the
spring doesn't go shooting out and get lost.
The
reason the spring is removed from the tensioner before the cam(s)
are disturbed is so it cannot get tighter either during the procedure.
Nothing you are doing during the valve adjustment would cause
a need for the tensioner to be tighter or looser than when you
started unless the cams were disturbed before the tensioner was
disabled by removing the spring. |
21. |
On
to the cam caps. The two right side caps, Intake
& Exhaust, are separate and will easily come off individually.
The two left side caps are connected by an oil feed pipe and must
be lifted up evenly, equally and together, keeping the pipe in place
between them. (I put the caps in the appropriate box on the FORM I
made so as to not goof up when re-installing them. They must go
into their correct places. The caps are marked, also.) |
22. |
The
cam chain tensioner bolt & spring are out, and the cam caps
are off - 8 cap "tubes" are accounted
for, right?! The cam chain is still attached on the left side, so
don't go nuts and try lifting the shafts up 1 foot, but you can
now lift the right ends of the cam shafts to gain easy access to
the shims. The shims sit in a "cup," and this cup can
be spun around until you find the notch where you'll use your tweezers,
or whatever you choose, to get the shims out. Oil under the shims
can create a slight "vacuum," so a slight amount of effort
will be required to get the shims out. (My preference is to use
a very thin jewelers screwdriver to pop up the shim, and a kelly
clamp to grab and pull it out.) NOTE:
As
with the clearances, keep very close track of what size shim was
at which valve - this is very important. I do
one at a time, write each shim size on the form, and then place
that shim in the appropriate box on the form. |
|
All
this is written assuming a full, 4 valve clearance check. Note
that the shims you removed were placed with the size numbers facing
down, this is so the cam doesn't wear them off.
Be sure to re-install the new shims number side down.
If
the size numbers ARE worn off, all is not lost. Obviously, if
you have a micrometer or digital calipers that would be the easiest
way to check the shim size. If you don't have either of these
measuring devices:
-
place the shim on a perfectly flat surface such as glass.
-
lay a shim of known size tightly next to it, edge-to-edge. (from
your spares or another bucket)
- slide a finger nail across the surfaces from one shim to the
other. Do this in both directions. A size difference will show
up when the fingernail catches on a shim edge. If it doesn't,
then you're probably good to go.
-
You'll want to scribe the center of an unmarked
shim to avoid this trouble the next time. Do it now based on the
assumption that you've gotten the size right, or install the shim
and measure the clearance.
NOTE:
A worn shim can be reused by flipping it over, and scribing the
size in the center of that surface. Scribing
is done in the center of the shim to avoid having a burr from
the scribing cause the shim to sit higher in the bucket. The center
of the shim typically doesn't contact the bucket. |
You
can do the math yourself, or save a lot of hassle and get a great
program called ShimCalc from Pat at IronJungle. The website is
at:
http://www.ironjungle.com/
(ShimCalc
Screen Shot)
You
will need three bits of information no matter how the figuring
is done - Initial Measured Clearance / Stock
Shim Used / Desired Clearance. Using
ShimCalc, you just plug in these numbers for each valve and the
software does the rest. (Stock Shim Used means the shim that was
in there when you used the feeler gauge a few steps back to get
the clearances.) |
I
bought the 16 shim set from Fred Hink at www.arrowheadmotorsports.com
to get started, and just replace the ones I've used so that I
never have to fool around when I need a shim.
I
use this shim storage box
to keep my spare shims rust-free, and oiled for use. |
When
you're all done with the job, I recommend you save the form with
all the information you've recorded for future reference. Also,
the shims you've taken out can be reused, generally. |
|
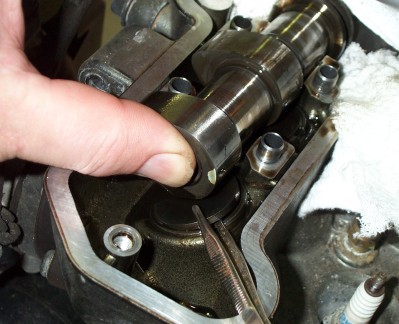 |
23.
 |
According
to what ShimCalc, or your math has indicated, put in the new shims
- shown in the picture above. With the cam caps
removed, you can lift the right end of the shaft to make room
for the shim to come out. Make sure the shims are clean of protective
coatings, dirt, or whatever. I like a light coat of fresh oil,
(which comes from removing them from the muffin tin), to get them
"started." Make sure the shims are completely seated
in the cup when you install the new ones.
You
can also break the oil suction, and get the shim out more easily
if you direct a short blast of air from an air nozzle at the cutout
in the bucket. Be ready to prevent the shim from becoming a frisbee
in case too much air is applied. |
NOTE:
It's a good idea at this point to pour some fresh, clean oil onto
the cam bearing surfaces, and the whole area in general - along
the shafts and such. |
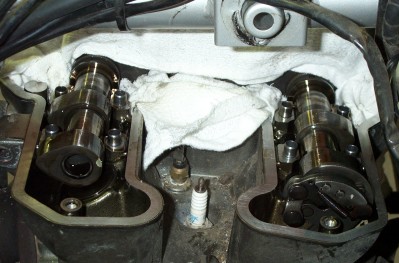 |
24. |
Making
sure the abyss rags are still doing their job, install the 8 cam
cap locators, if necessary. |
25. |
Put
all the cam caps back in place, taking care to not disturb the pipe
between the left side caps, and turn the bolts down finger tight.
Make especially sure that on the left side you've correctly placed
the caps so that they fit correctly over the ridge of the shaft
on the chain sprocket side. Getting these two "connected"
caps in place can be a little troublesome, don't force them! |
26. |
Tighten
the cam caps in the following order: (1) Left Exhaust - front bolt
and then rear. (2) Right Exhaust - front bolt and then rear. (3)
Left Intake - front bolt and then rear. (4) Right Intake - front
bolt and then rear. The torque spec is: 12N-m / 1.2kg-m / 104in-lbs
=> NOTE: That's
104 INCH pounds. |
27. |
You
can safely remove the rags now. |
28. |
Re-install
the cam chain tensioner spring and bolt into the plunger body. Try
to keep the spring as straight and even in the hole as possible.
You'll hear the teeth ratcheting out as the spring is compressed
into the hole by the bolt. |
29. |
Now
you're all set, with almost everything re-assembled, except for
the valve cover. It would be a good idea to give it at least 2 or
3 full spins and re-check clearances to make sure all is as it should
be. Remember, counter-clockwise only, and watch the stroke as in 18 to be
sure you're correctly at TDC. |
|
You
should be all set, but if something somehow went wrong, you'll need
to restart at step 20. Remember the abyss! |
|
30. |
Clean
the top of the engine and the bottom of the valve cover of any
silicone that may be on them. Use your fingernail to
do this, not a scraper or any other tool - it's important to not
damage the machined surfaces.
Alternatively,
you can use a plastic scraper of the type that fits into a razor
scraper holder. Also, you can form pieces of plexiglass to do
the job. If you don't have scrap plexiglass, check with a glass
shop to see if they have any in their trash bin. Be sure to clean
the plexiglass of any shavings or bits left hanging on. |
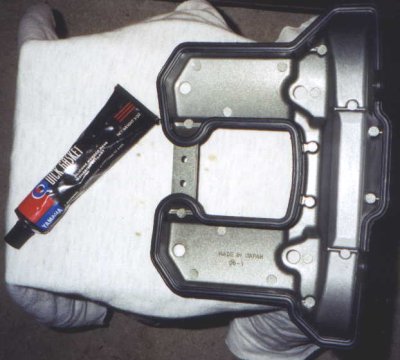 |
31. |
Use
a small amount of non-drying silicone all around
the rubber gasket surface of the valve cover. Be sure to wipe
off any excess from the inside and outside edges of the cover.
Again, you want very little here, just enough to lightly coat
the surface and create a seal.
I
apply a small line of the silicone all the way around the gasket,
then place my index finger on the top of the gasket, my thumb
on one side of the gasket and my forefinger on
the other side. I then just run around and around
the entire gasket / cover surface until I have complete coverage
of the gasket using the smallest possible amount of silicone.
Be
sure to get the silicone all around the two "circles"
on the left side. |
32. |
Re-install
the valve cover starting from the left side; it won't go over the
chain sprockets if you try from the right side. Go carefully and
slow here, taking care to avoid any contact with the coated gasket. |
33. |
Once
the valve cover is in place, you can thread in the four cover bolts
finger tight. I would suggest tightening in an "X" pattern,
as in the number 16 removal step. Once you're ready
to torque the bolts, you should do so only about 1/4 turn per bolt,
per time, to avoid "warping" the cover. The torque specification
is: 7.8N-m / 0.80kg-m / 69INCH-lbs |
|
From
this point on, re-assembly should be pretty obvious. Before you
get the gas tank back on, this would be the time to check the spark
plug. |